I always wanted to convert some type of vehicle to electric propulsion. I thought about a car or truck but the cost and complexity was more than I wanted to get involved with. I thought about a boat to cruise around the harbour, but the range and Time on Water was poor with the number of batteries I was willing to buy. GoKart…no use for one and no where to ride it. Motorcycle had me for a while but the limited range was a deal breaker….
So lets see…I wanted to limit myself to 48V or 4, 12V batteries = HEAVY
With 48V , depending on batteries, I’m looking at 1-2 hours or under 20 miles with a road going vehicle.
Sure a car or truck or boat has enough room for batteries, but a motorcycle doesn’t……Unless you get involved with expensive LiFo batteries…Much more on this in a minute
So….What kind of vehicle can benifit from lots of weight….doesn’t need a lot of range or hours…..and has room for lots of batteries?
A TRACTOR!…….Tractors love weight…WEIGHT = TRACTION!…..Most folks that use tractors actually add heavy weights to the rear tires. Either externally or they fill the tires with anti-freeze….And they add a Weight Bar and load it up with “Suitcase Weights”….In a tractor, weight is good!
Tractor that are used residentially are used quite infreaquently. Maybe an hour or two a week for 30-35 weeks here in New England…..And there is plenty of time between use to charge the batteries. No Quick Charge ($$$) system needed.
In a residential setting range isn’t an issue. How many hours you can use the tractor is more important. 1-3 hours would be plenty in most cases.
So a TRACTOR it is!
I recently became enamoured with old Garden Tractors. As a Corona Virus project to keep myself occupied I bought a rundown International Harvester Cub Cadet 782 and refurbished the whole thing. You can read all about this project here:
But I wasn’t about to start tearing this tractor apart to convert it to electric. I needed to find another victim.
Searching Craigslist I found a John Deere 214. Looked to be in good condition….And it didn’t have a motor…..$200…..PERFECT! Hook up the trailer and go get it only a couple miles away.
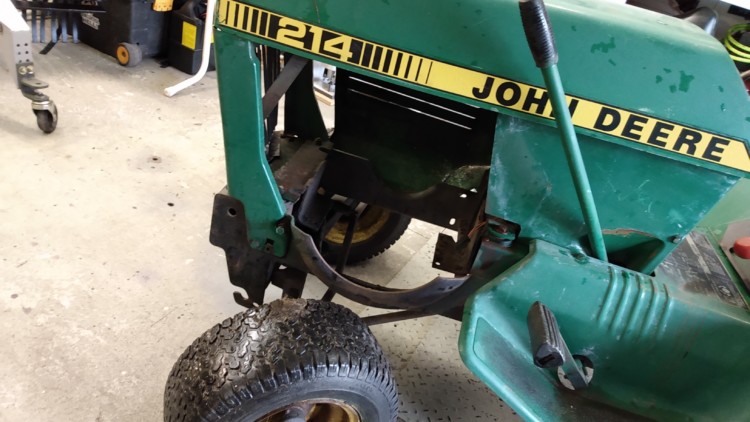
As I was preparing to order parts to convert the John Deere, and spending hour upon hour on the internet and especially YouTube to see how other folks accomplished similar conversions, I realized that the John Deere “GARDEN” tractor, with a Horizontal motor shaft would be more difficult to convert than a more simple “LAWN” tractor that has a vertical motor shaft.
Just so happens my Son-In-Law has a Toro LX-460 with a bad VERTICAL shaft motor! The tractor is in fantastic condition, but the motor needs more parts to get it running than it is worth.
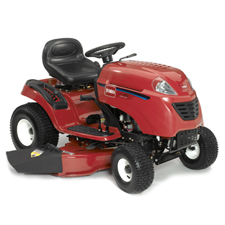
And this Toro will be MUCH easier to convert for my first EV conversion.
So….Lets tear it apart…..Anything and everything that has anything to do with the Internal Combustion Engine (ICE) is removed. Engine, wiring, throttle, gauges…….GONE!
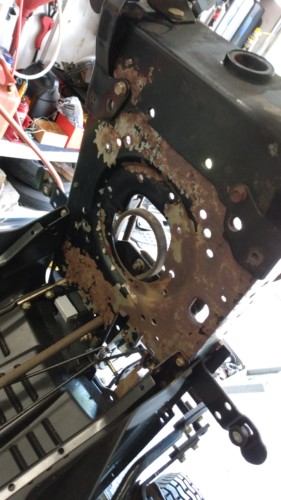
We will retain the transmission and the belt drive system as this tractor conversion will be a constant speed motor with the ground speed controlled by the tractors transmission.
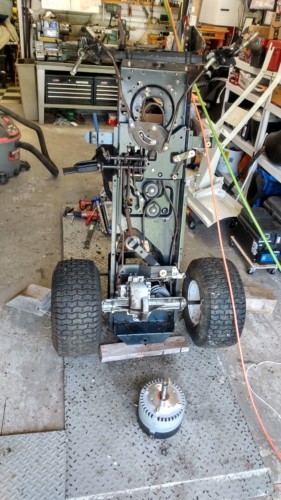
I could have used a DC MOTOR CONTROLLER and controlled ground speed by increasing or decreasing the speed of the motor. But that would add over $500 to the project for a controller and a throttle and add a bit more complexity. I can always go to this design in the future.
THE MOTOR: Research showed that many, if not most folks doing a tractor conversion were using a motor actually designed for just this. MOTENERGY ME-1004……32 pounds / 13HP / 3300RPMs
” This is a Permanent Magnet, Brush Type, DC Motor with Neodymium Iron Boron Magnets. The 1″ shaft is similar to the shaft on most Lawn and Garden Tractor engines. This motor is perfect for an engine replacement on a Lawn and Garden tractor when converting the tractor to electric propulsion. No motor control is necessary for an engine-swap, but you will need to add a Contactor, Fuse, and 48 VDC batteries. Timed for counter-clockwise rotation (can be changed to clockwise). …….Capable of 200 amps continuous, and 500 amps for 1 minute. The efficiency is 90%. Power 6.4 KW continuous @ 48V”
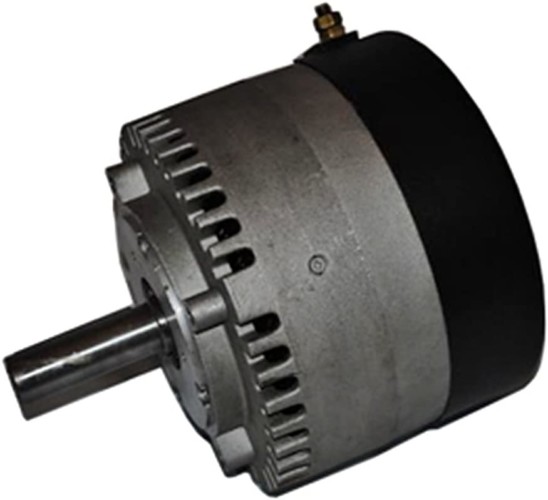
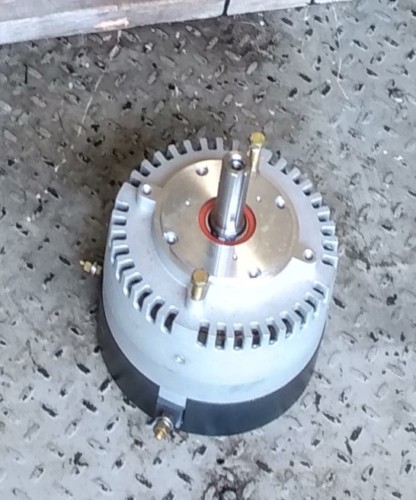
As the description from EVDrives website says, we need a CONTACTOR…
The SOL400 from EV Drives or the MZJ-400A from AMAZON (They appear to be the same) was chosen
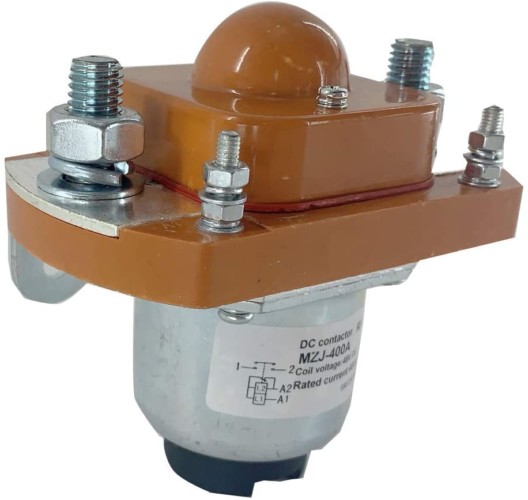
BATTERIES….The best deal on earth for high quality batteries are the Duracell AGM, Group 31, 12V , 110Ah DEEP CYCLE batteries from Sam’s Club. I bought two of these 5 years ago for my travel trailer and I tested them just a couple weeks ago and they are still 100% perfect! Five years ago they were $179 each and in 2020, they are still $179! Everywhere else this same battery or similar performance are $250-$350 each! Four were purchased using some of my Trump stimulus $$….I really wanted to build a Lithium battery pack. But the cost would have been three times as much as the AGMs with a BMS (battery maintenance system) and a special charger. Not this time!
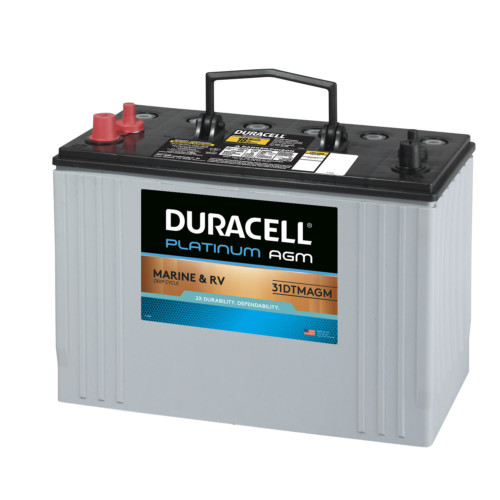
OK, so now I got MOTOR….CONTACTOR….BATTERIES…Lets build this thing!
First we need to mount the motor. My scrap pile offered a near perfect piece of plate steel. Needed to cut a hole in the middle for the motor shaft and the pulley. Easily done with a 4″ hole saw.
My milling machine with a DRO (Digital Read Out) made locating the four holes to bolt the motor to very easy
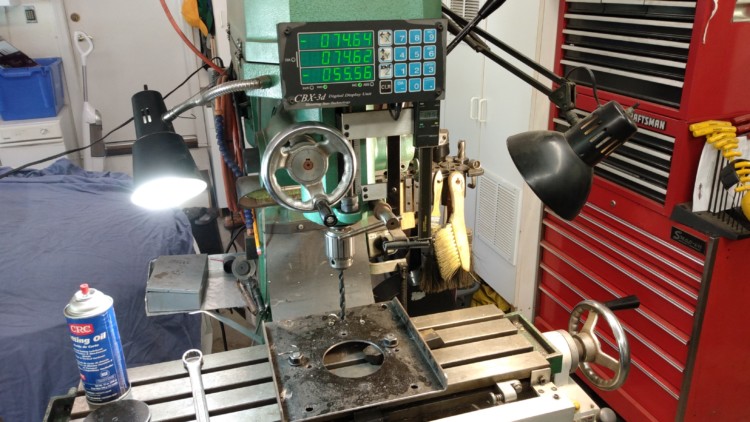
The motor was bolted to this plate
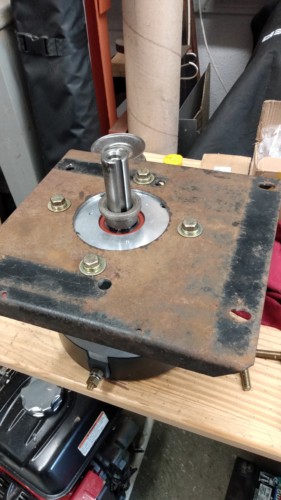
And the plate bolted to the tractors frame, in the exact same place the ICE was bolted…..Interesting to note, this plate had a few holes already drilled and two of them matched up perfectly to the holes in the chassis! I should have gone out and bought a lottery ticket…My luck was running good!
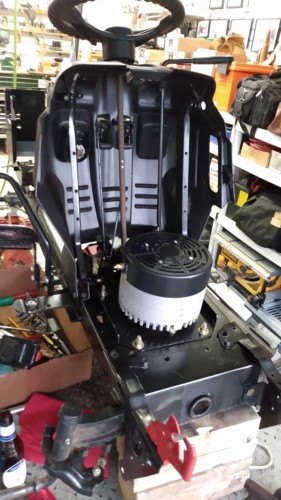
The pulley was installed, although I had to turn a spacer as the motors shaft was just a bit longer than the Toros pulley bore
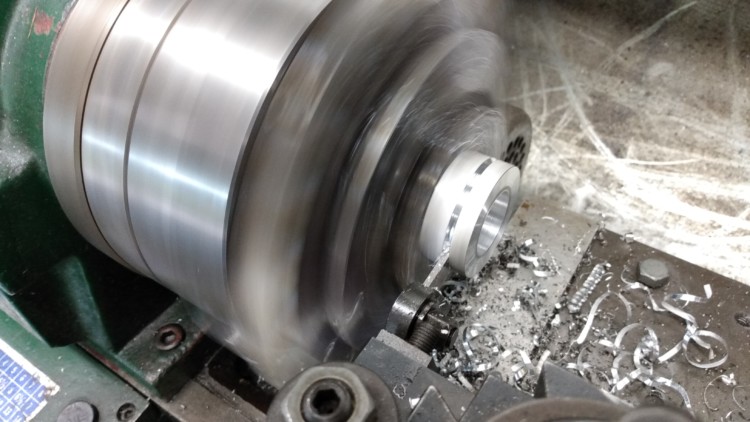
So, motot installed….Belts were replaced and laced up…
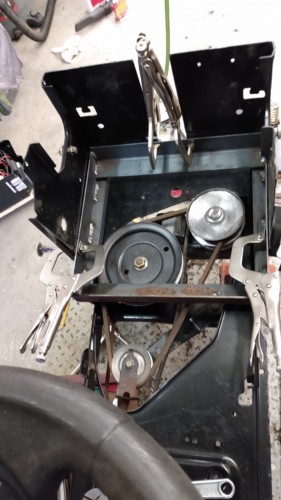
Where to mount the four, 80 pounds each, AGM batteries. Most conversions I read about had all four batteries in the front of the tractor. I was extremely concerned about 320# over this “Lawn” tractors front axle. And loss of traction with so much weight forward.
Sitting on my “Pondering Stool” in the shop…..and staring at the tractor, it occured to me with a little modification and some cutting and welding, I could get two batteries under the seat, and two batteries a bit further back from the front axle by placing them over the motor…
An angle iron support system was welded up for the rear as this area needed to be widened by about 3 inches. The original under seat starting battery compartment was split to widen it also.
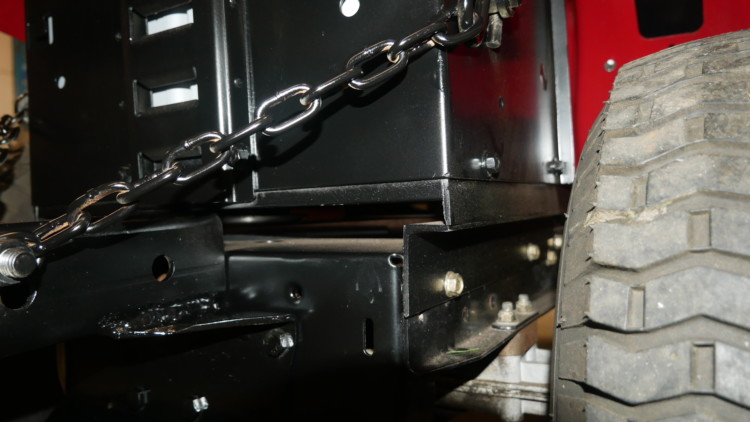
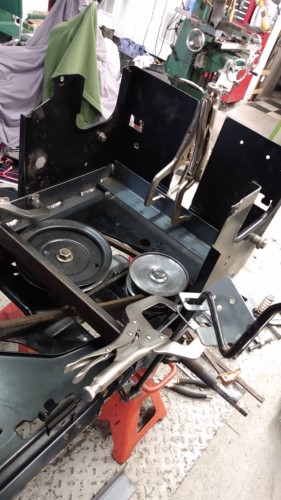
To fill in the gap by splitting the battery box, my scrap pile offered up a piece of “E-TRACK” ….This will allow me to utilize hooks and rings that snap into the E-Track for carrying stuff….
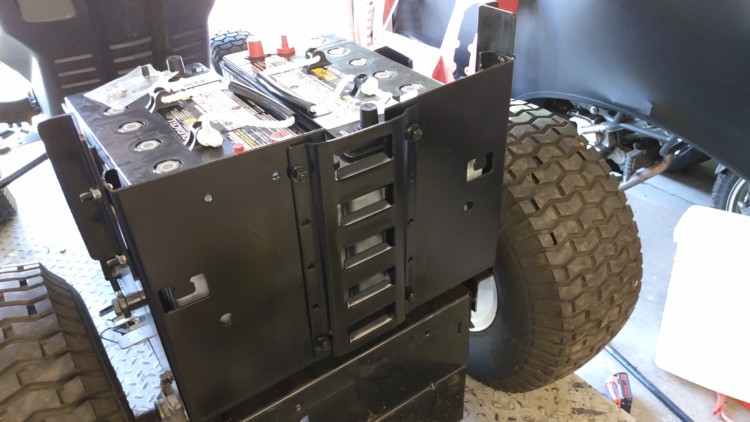
Everything welded up and bolted together we can move to the front.
Lots of height under the hood allowed two batteries to be place directly above the motor. Once again an angle iron support structure was welded together and bolted to the tractors frame…
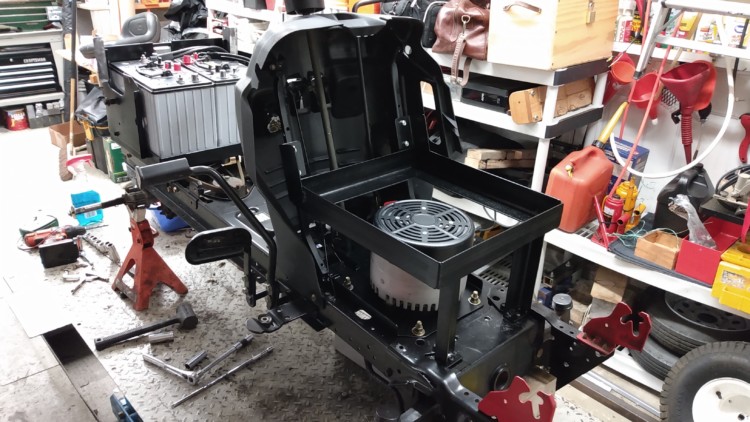
I designed this fixture with enough space so there was a 2′ gap between the batteries and 1.5″ above the motor so the the motor could be ventilated properly.
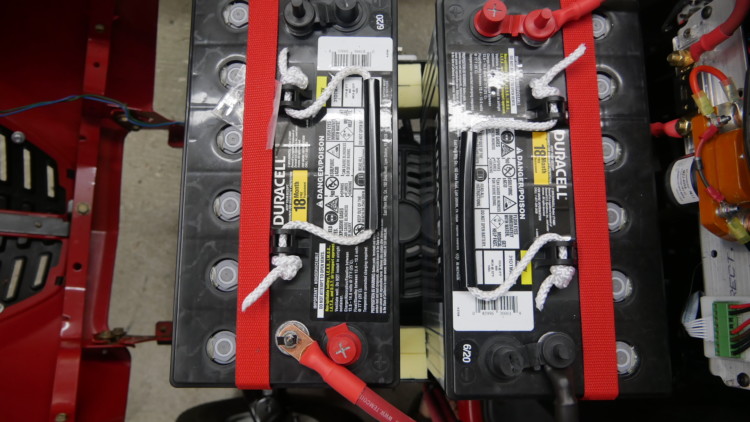
But just to be sure, I installed a large, 129CFM, computer fan on the motor and the ability to watch the motors temperature with a digital remote “Aquarium” thermometer. (BTW…In the first couple hours of use, the motor temp never went above 115 degrees)
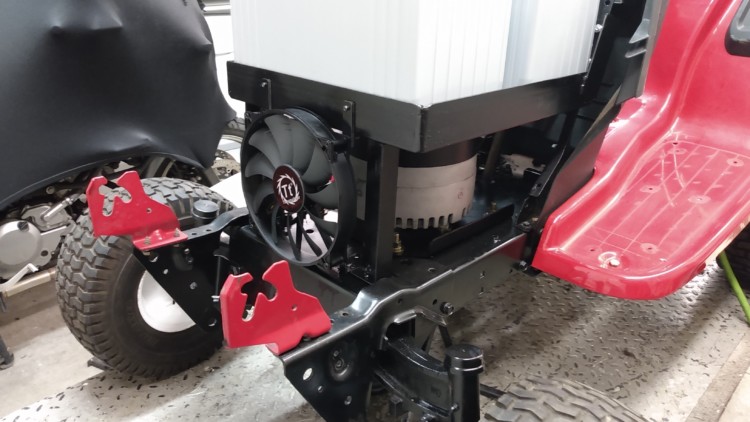
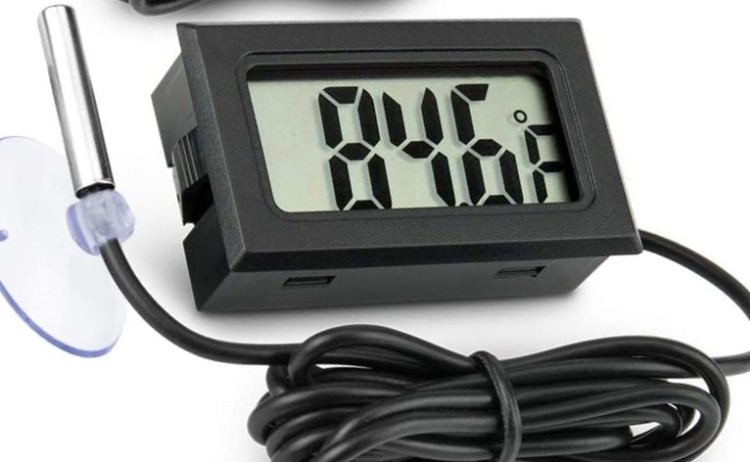
Ok….Motor installed….Batteries Mounted…Lets move on to wiring this Bad Boy!
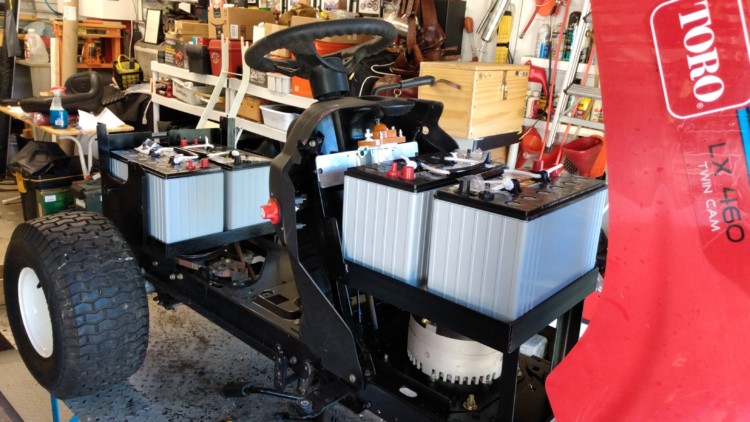
A bracket was fabricated to mount the 400A fuse, the 400A contactor and the circuit board for the battery monitor. A simple piece of aluminum bolted to the dash supports.
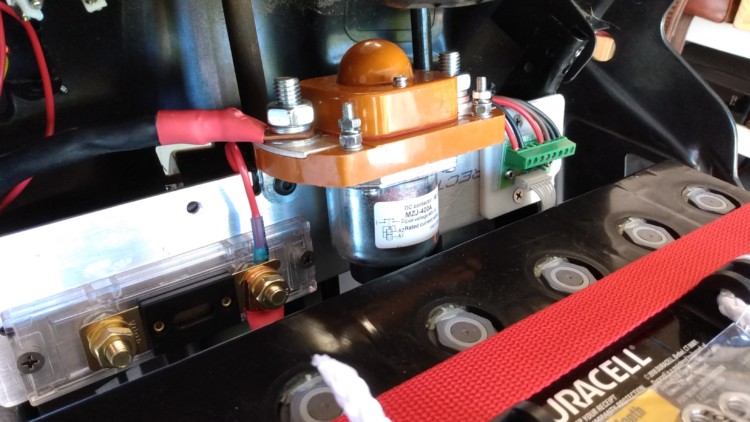
The battery monitor digital readout was cut into the dash board
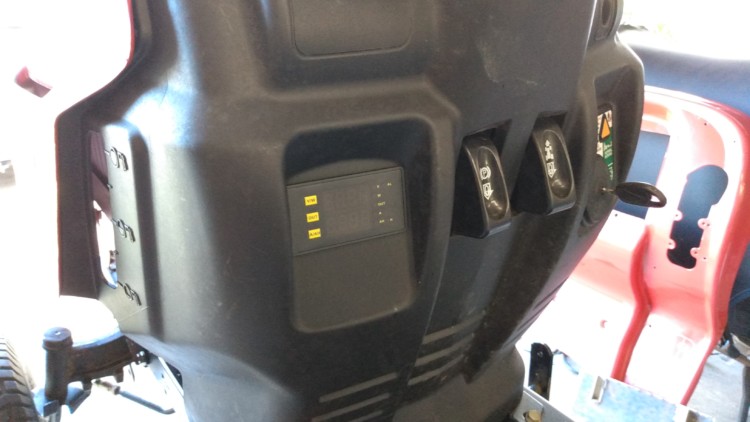
The 12V fuse panel, 12V ground buss, the 500A Shunt for the battery monitor and the 48V DC to 12V DC converter were installed on the right side of the front battery mount. The Shunt and the 12V ground buss were mounted on pieces of PVC plastic to isolate them from the chassis. The chassis was not used for any grounding. All grounds, both 48V and 12V had direct returns……More bettah!
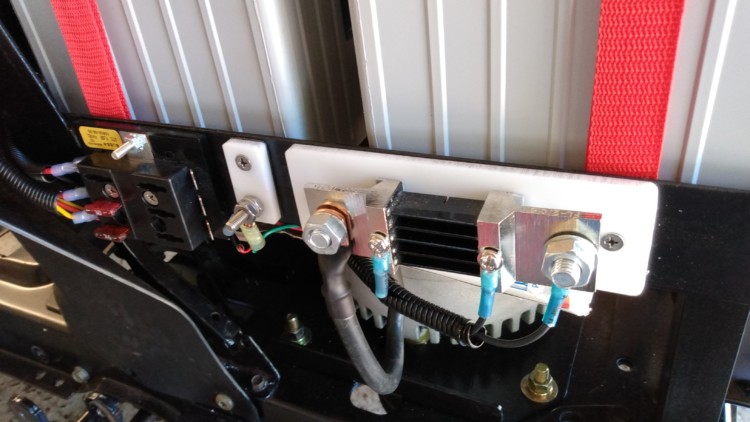
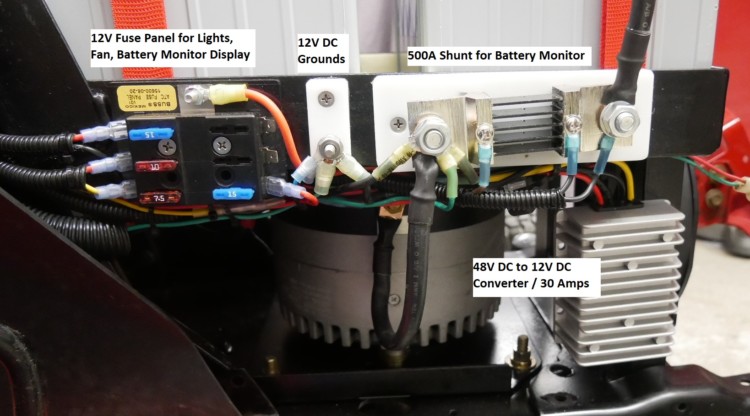
The shunt you see in the picture has a high current wire coming from the negative side of the battery bank and then ALL other 48V negative feeds are attached to the other side of the shunt.
The low current wires you see coming off the shunt attach to this connector board which in turn feeds info to the battery monitor panel
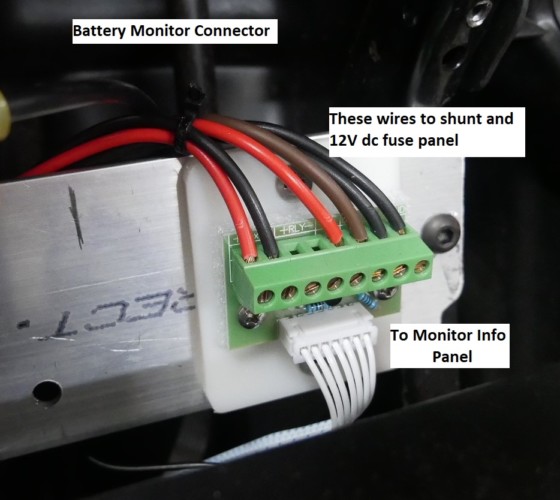
The ICE throttle was removed and a piece of ABS plastic was heated up and molded to cover this hole. Three waterproof toggle switches were installed for Lights, Cooling Fan, and a third for future use. Two indicator lights were installed for fan and running light notification.
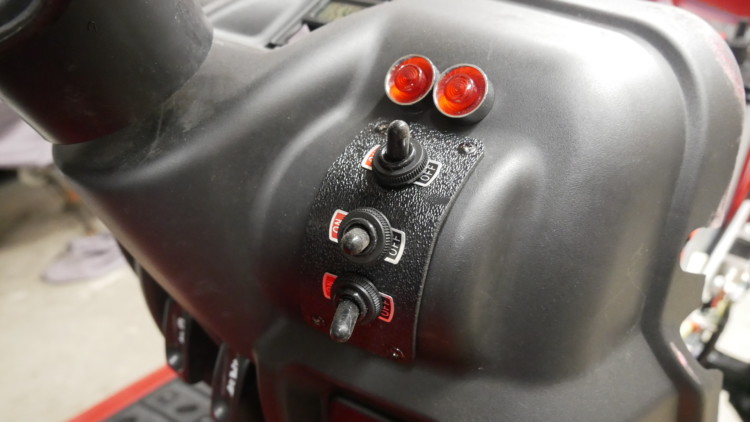
The 400A “DEADMAN” switch was installed along with an indicator light. This shuts all electricity down when the tractor is not being used and in case of an emergency
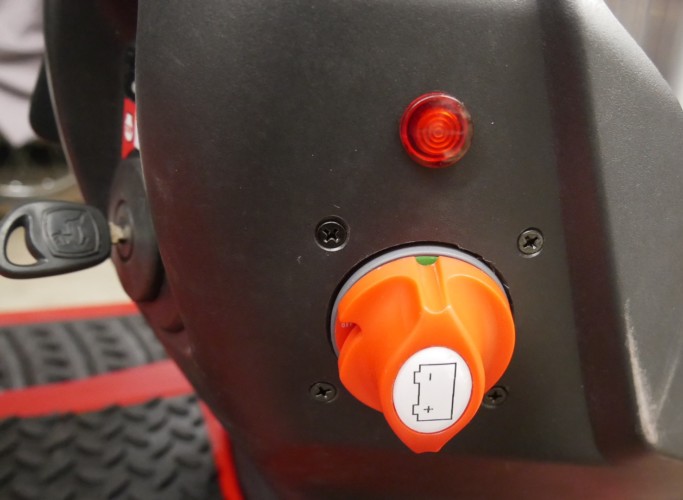
To actually energize the motor, I used the existing ICE ignition switch. This switch simply completes a low current circuit to the high current contactor to energize the motor. I made a little label in “word” on the computer and used my wifes nail polish to ahere and weatherproof it. “RUN”
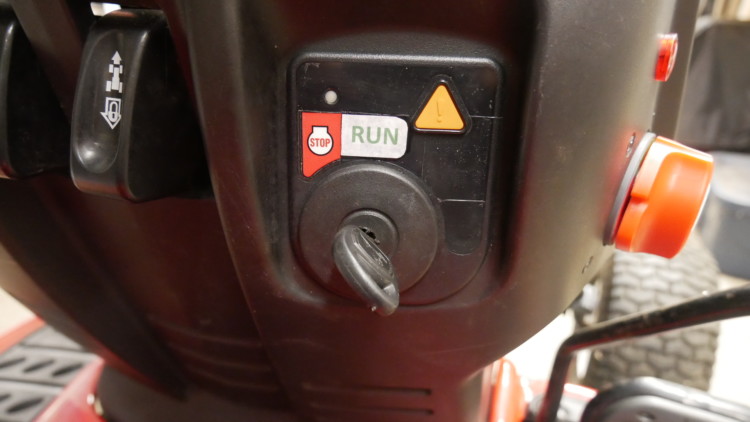
Lastly the remote, digital thermometer was installed in an existing space on top of the dash. It fit without modification….Another “WIN” and a little filler panel was fabricated out of ABS to fill below it. The temperature probe was attached to the side of the motor, away from the fan, with Gorilla Tape.
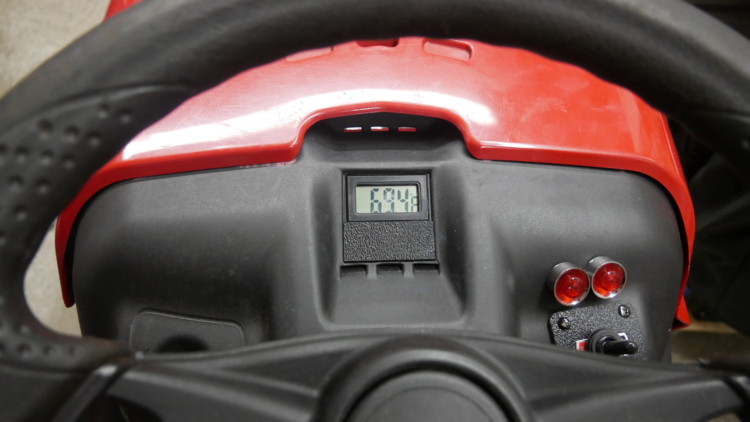
All that is left is Primary 48V high current and 12V low current wiring
The 48V stuff was wired with 1/0 Copper Welding cable. Huge wire to handle this type of current. I purchased a hydraulic crimper to attach the crimp connectors and heat shrinked all of them
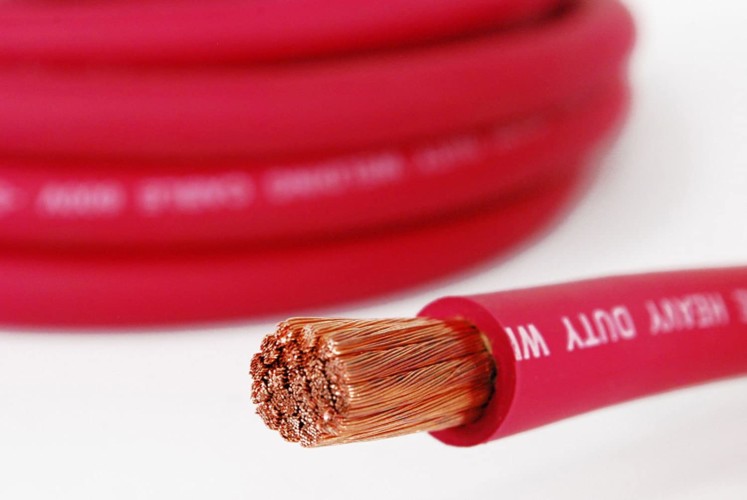
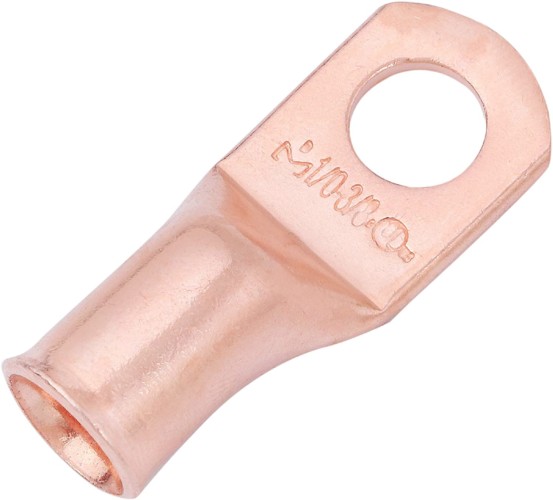
All the 12V wiring was accomplished with marine grade, 12g tinned copper wire using heat shrink, crimp on connectors
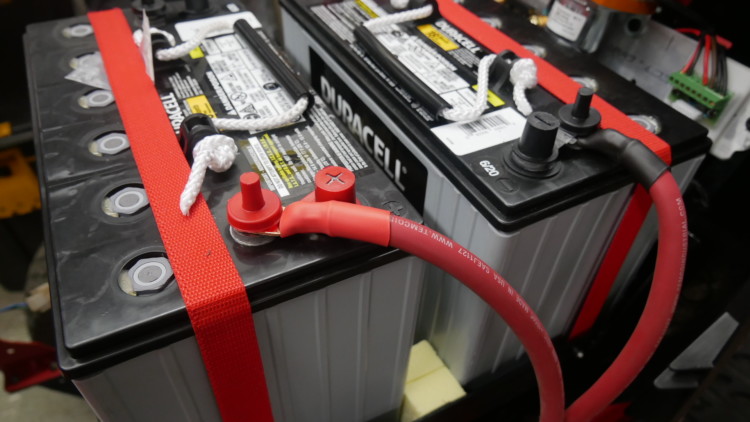
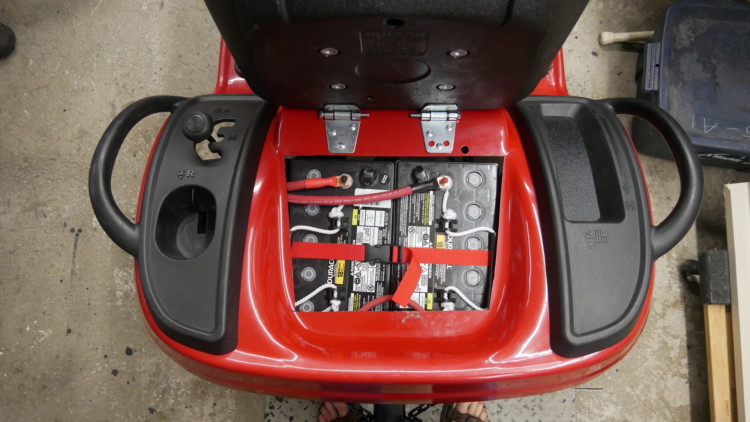
Battery tie downs were made and installed

Here is the actual wiring diagram for this project. If you can’t read it and want me to send you a copy, email me with the request. rvb100@comcast.net
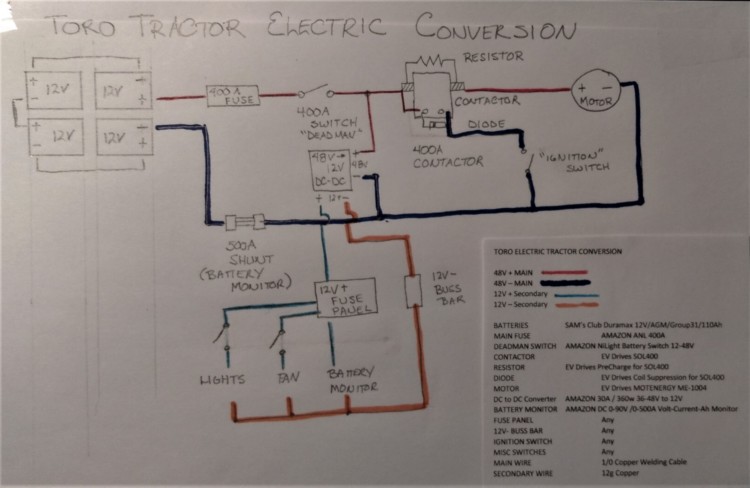
The area that the mower lift lever was filled in with a piece of ABS plastic.
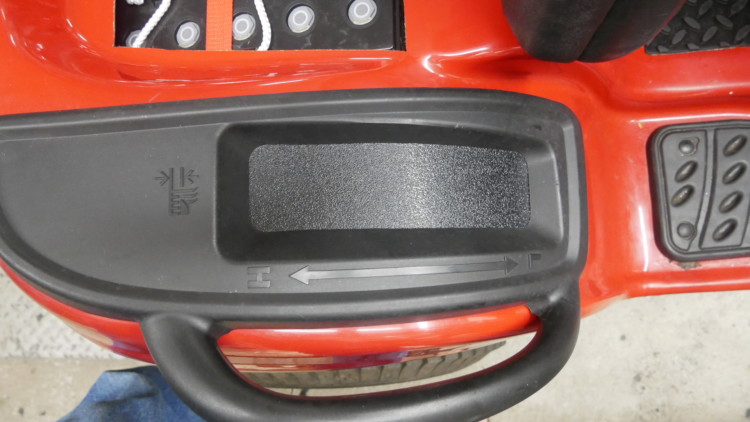
To move trailers around my property and to pull my York Rake and garden trailer, I needed a receiver hitch….One was fabricated and installed. I like the chains….It gives it Three Point Farm Tractor Cred!
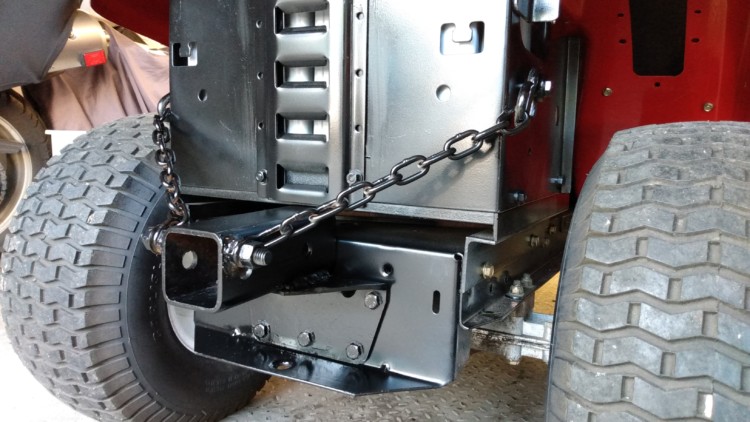
Tractor body panels were reattached and a test ride was completed..FANTASTIC! Worked perfectly. Amazing amount of power. With all that weight, zero wheel spinning…….Unless I wanted to…. 🙂
Here is a test ride and a full walk around video
That about does it! I think my first EV project turned out pretty good!
WHAT’S NEXT…….Well…There is great concern that this small “Lawn” tractor’s rear differential and transmission will not be able to handle all this instant torque for very long. I tend to agree…..I’m glad I didn’t sell that John Deere “Glider” I have out back as I can see all this stuff moving over to that “Garden” tractor at some point…..Stay Tuned!
I get a bunch of questions from friends and neighbors:
Are you going to mount the cutting deck?…. No. I’m building a front mounted cutting deck that will have its own motors and a LiPo battery system. This will offer me the opportunity to try building a Lithium battery pack from parts. And front mounted deck will be much more manuverable on my property.
How long do the batteries last ?……. I’m not sure. I’ve been driving this thing around for a few days. Pulling a small trailer full of firewood and dirt, letting grandkids ride it. Showing neighbors and relocating a 2000# trailer up a pretty steep hill. All totaled about an hour and a half of use and I still show 85% battery life! I’m going to guess I can get three hours of this type of use. Now if it had the mover deck running off the tractor’s motor and battery, I estimate 45 minutes of use before batteries should be recharged.
How much did it cost ?……
TORO LX-460 FREE
BATTERIES $716.00
MAIN FUSE $ 7.49
DEADMAN SWITCH $ 13.49
CONTACTOR $ 59.18
RESISTOR $ 9.99
DIODE $ 8.99
MOTOR $606.85
DC to DC Converter $ 39.99
BATTERY MONITOR $ 30.50
FUSE PANEL $ 12.39
12V- BUSS BAR $ 1.00
IGNITION SWITCH FREE
MISC SWITCHES $ 9.70
MAIN WIRE/CONEC $ 63.25
SECONDARY WIRE $ 20.00
MISC STEEL/HDWR $ 50.00
TOTAL $1639.12
YIKES!!!! Way too much. But what the heck….This is my enjoyment. Some folks gamble away this much in minutes! And as my friend Tom always says, “There are no ATMs in Heaven…..or Hell!”
I hope you enjoyed this article. Let me know……Be sure to check out all the other wastes of my money…… www.rvbprecision.com
UPDATE!!!!
Well……I’ve been driving the daylights out of the electric tractor. It is a blast to use. The neighbors love it….. BUT…..It ain’t going to last. The transmission is now very hard to get into gear and the differential is making noises. It seems these smaller LAWN tractorts are simply not up to the task of these high torque DC electric motors………….So, “Plan B”….Everything will be moved over to a John Deere 214 “GARDEN” tractor. Everything is bigger and stronger on this tractor.
This morning I got up early and looking at Facebook Marketplace a fellow had three tractors for sale….”Make Me An Offer”….He had a complete 214 and I offered $100…..ACCEPTED! An hour and a half away and off I go!
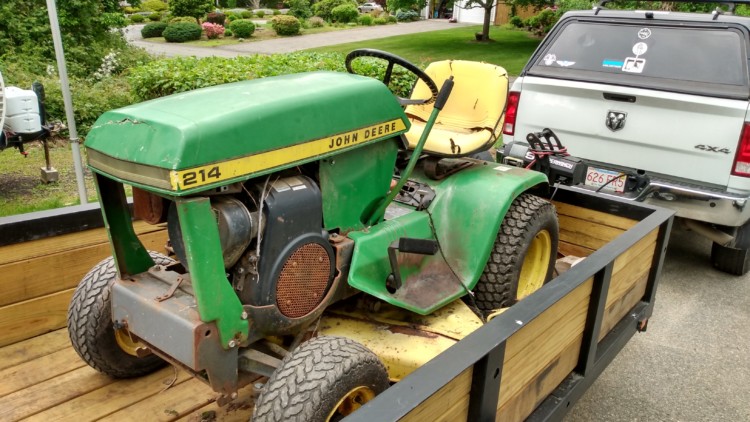
So now I have lots of JD 214 parts, and what I don’t use I’ll sell off to recoup some of my expenses…..
UPDATE-UPDATE 6-20-20
I finished taking all the parts from the Toro and installing them into the John Deere 214. New tires, paint, decals…..I’ll be writing an article all about this conversion soon…..But for now, here are a few videos…
Be sure to check out my other articles at www.rvbprecision.com
Thanks!
Pingback: GARDEN TRACTOR TO ELECTRIC CONVERSION / JOHN DEERE 214 | RVB Precision